Is the Garment SAM a Hypothetical Data?
/ Industrial Engineering /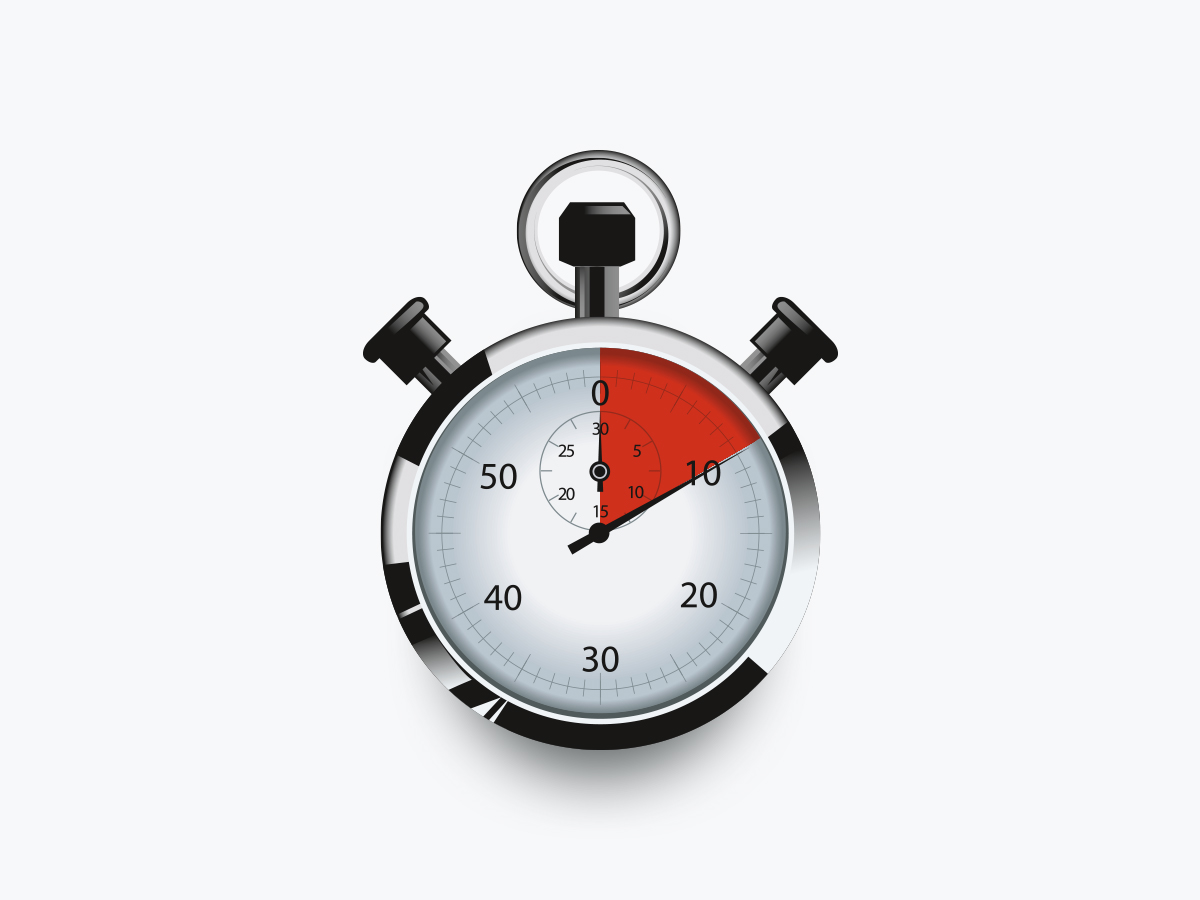
The question is the title of an article by Prasanta Sarkar from his valuable OCS blog. Origin of the question is a comment on a recent article on OCS:
“I would like to add one important point regarding SAM value. In the definition of standard time, it mentioned that That is qualified worker. Worker is frequently changing in garment industry. There is no permanent labour for same operation in a line. Some days he is going to remain absent. He will flip the job, there is change in method of new operator. So, I think SAM value is just hypothetical. In the real world, it is showing quite far result. SAM value is just refence. You need to decide your own SAM for each garment you CMT. Still that is going to vary.”
-> Full article available here
What it means “standard” ?
“Usual rather than special” says the Cambridge Dictionary.
Rarely the focus is on the “qualified” but more on “average” worker, when we are talking about standard time. The “worker” by default should mean that the person knows how to do what she / he do.
When the “usual” it comes into the field of mathematics then it became “average”, following a kind of statistical distribution.
Our usual life is running around the Gauss distribution, in all domains.
Regarding the hypothetical side of the SAM I can agree if I’m looking only from the pure mathematical side and the following example explain simple.
In a team are 6 members with age 22, 24, 25, 28, 30 and 33 years. The average age is 27 years but in fact nobody is 27. As we increase the team member numbers than more and more will have the age closer to the average but isn’t granted to have anybody with the age exactly equal to the average.
With the SAM the situation is the same and it’s coming from the “average” worker.
The “average” is a concept, maybe in a manufacturing unit with thousands of workers nobody can fit exactly as “average” but most of them are enough close (with a + /- epsilon) to be considered it.
“Average” worker is an “average” human with all of capabilities criteria. This is the reason why the standard time is the (same!) “standard” in India, Bangladesh, Columbia, Romania, Germany, Ethiopia … with the condition of “… the same circumstances …”.
Same circumstances mean similar working place, same equipment, same transportation system, same fabric, same operation, same all other things but different worker.
Here is the key of the efficiency
Nobody says that the SAM is the ideal, the best, the ever-possible minimal execution time for the defined operation.
Doesn’t matter how is established, by classical time study or using a PMTS (both provides the same number, up to the 4th decimal digit, if are performed by professionals).
The SAM is the standard time for that defined operation, in that conditions, independently of the worker.
If I want to improve the SAM I should improve the conditions as the operation, model, fabric is the same and it not depends on human.
Unfortunately, in practice the usual condition improvements are ending with the improvements of the machine / equipment, which means an additional investment (more, less, doesn’t matter, but important).
Many times, this could result in illusions because the better equipment improves the productivity without to have any influence on the efficiency.
Using a step by step, detailed analysis of the full operation, analyzing all its detailed motions the IE could find – and a good professional will find – that motions what should be changed to get a better SAM.
Important : better SAM means the corresponding level of less efforts required from the worker!
The action requires first the will of the IE, some efforts to concentrate and innovation sometimes. A series of solutions already exists in the industry which require only to apply them (for example: introducing the bundle system, use some boxes to transport the pieces, store the small pieces in a storage hole close to the operator hands and many-many others).
Each of these changes could mean individually just few seconds – we like to say “is nothing” – but accumulated the number of seconds, saved only for one operation, could be more than relevant.
Just extrapolate the few seconds saved on one operation, resulted from changing the circumstances, on all operations of a style, and more, extrapolate it to the whole factory.
In one of my writing before, “To blink or how not to blink?” , I described what could mean to save on each motion a time equivalent with a blink (0.0005 min) : in case of a unit with 800 workers this means 120.000 USD turnover per year.
Hypothetically standard time
To discuss the existence and the applicability of the standard time is like to discuss about the existence of the Moon. For me not exist because I’m going to sleep earlier, when the Sun is up.
During the years and hundreds of factory visits from all over the world I had the chance to see in many places the way how the operation execution times are established.
The very usual is to add / subtract just using the pen (Excel) an imagined amount from an already existing time of a similar operation (is another question how the “reference” time it was established once).
Sure, the procedure is working until the factory has the profit level enough high, but this procedure is one of the killers of the added value. For example, today for the RMG industry in Bangladesh this is the biggest problem (not recognized and not accepted yet), accumulated during many years: execution of low added value products with low responsibility for the labor costs.
But the same approach still exists in my country, Romania, in many factories with relevant history and reputation in the past. The difference – comparing with BD – is in the starting efficiency level and the products executed, no difference in procedures.
As the products are with higher added value still exist some space to not really care of the SAM.
They feel, see, the pressure but in case of the discussions regarding the SAM the answers are the same as 20 years before : our situation is special, the workers fluctuation is high, we manufacture complex styles, the delivery deadlines are to short … and the list could follow.
The blinks are flying and when no more space because of the prices then is already late, the solution is to close the factory.
Nobody will recognize the factory close as the result of own inefficiency, all the time the brands and the government will be culpable, as in any other place in the world.
SAM isn’t enough
Isn’t it enough to have the accurate SAM. Is necessary but isn’t sufficient.
To get executed the operation in the time indicated by SAM the worker should be trained, and the progress should be monitored.
I think here are located the bulk of the problems. Here are the very visible advantages to use a PMTS to define the SAM.
The methods defined with PMTS , like timeSSD® (www.timessd.com ), have by default a step by step description, explained in detail and on the workers language. I know, many times require high efforts to convince the worker to follow the method as it’s described, but that is the only way to reach the SAM with average effort.
No chance to have the same detailed, structured and consistent description of a method without PMTS … and I want to avoid now to discuss regarding the effort differences, required from the IE side, to have the SAM using the classical time study.
Monitoring the efficiency level of the workers gives the possibility to show to them their real levels, to know it. In addition, the IE could find and step in if a problem is observed. The speed to find out the origin is a matter of the detail of data collected from the shop floor.
Using the SAM the planning and balancing become smoother and faster avoiding the bottlenecks, the efficiency figures monitored will catch the attention to the places on the shop floor where are the real problems. When the problems are known is only a matter of know-how and time to find the right solution (no matter if are coming from the flow or from defected machine or worker’s missing knowledge …).
Without SAM = without standard time = the whole production is a cloud
Every responsible see what and when she / he want, all the time exists reasons what to explain regarding any “why” question and the efforts and times are consumed for explanations, finding arguments which are fare away from the reality. Because nobody has data about the real status, nobody knows the reality.